11.7 The following heat sink consists of a 1 m tall central tube and 12 radial fins that are uniformly distributed every 30°C around the central tube. The central tube has an outer diameter of 0.4 m and an inner diameter of 0.36 m. Each fin is 0.048 m wide, 0.4 m long, and 1 m tall. The vapor temperature inside the tube is 315°C with a heat transfer coefficient of 2.94 x 105 W/(m2°C). The surrounding air temperature is 0°C with a heat transfer coefficient of 40.88 W/(m2°C). The heat sink is made of aluminum alloy with a thermal conductivity of 175 W/ (m K), a density of 2770 kg/m³, and a specific heat of 870 J/(kg K). Optimize the fin width W and the fin length L to minimize the use of material while achieving a minimum heat dissipation of 75 kW per unit length. The design variables W and L have the following range of variations: 0.03 m < W<0.052 m, and 0.2 m
11.7 The following heat sink consists of a 1 m tall central tube and 12 radial fins that are uniformly distributed every 30°C around the central tube. The central tube has an outer diameter of 0.4 m and an inner diameter of 0.36 m. Each fin is 0.048 m wide, 0.4 m long, and 1 m tall. The vapor temperature inside the tube is 315°C with a heat transfer coefficient of 2.94 x 105 W/(m2°C). The surrounding air temperature is 0°C with a heat transfer coefficient of 40.88 W/(m2°C). The heat sink is made of aluminum alloy with a thermal conductivity of 175 W/ (m K), a density of 2770 kg/m³, and a specific heat of 870 J/(kg K). Optimize the fin width W and the fin length L to minimize the use of material while achieving a minimum heat dissipation of 75 kW per unit length. The design variables W and L have the following range of variations: 0.03 m < W<0.052 m, and 0.2 m
Principles of Heat Transfer (Activate Learning with these NEW titles from Engineering!)
8th Edition
ISBN:9781305387102
Author:Kreith, Frank; Manglik, Raj M.
Publisher:Kreith, Frank; Manglik, Raj M.
Chapter10: Heat Exchangers
Section: Chapter Questions
Problem 10.51P
Related questions
Question

Transcribed Image Text:11.7 The following heat sink consists of a 1 m tall central tube and 12 radial fins
that are uniformly distributed every 30°C around the central tube. The central
tube has an outer diameter of 0.4 m and an inner diameter of 0.36 m. Each fin is
0.048 m wide, 0.4 m long, and 1 m tall. The vapor temperature inside the tube
is 315°C with a heat transfer coefficient of 2.94 x 105 W/(m²°C). The surrounding
air temperature is 0°C with a heat transfer coefficient of 40.88 W/(m2°C). The
heat sink is made of aluminum alloy with a thermal conductivity of 175 W/
(m K), a density of 2770 kg/m³, and a specific heat of 870 J/(kg K). Optimize
the fin width W and the fin length L to minimize the use of material while
achieving a minimum heat dissipation of 75 kW per unit length. The design
variables W and L have the following range of variations: 0.03 m < W<0.052 m,
and 0.2 m <L<0.45 m.
W
Expert Solution

This question has been solved!
Explore an expertly crafted, step-by-step solution for a thorough understanding of key concepts.
Step by step
Solved in 3 steps with 3 images

Knowledge Booster
Learn more about
Need a deep-dive on the concept behind this application? Look no further. Learn more about this topic, mechanical-engineering and related others by exploring similar questions and additional content below.Recommended textbooks for you
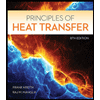
Principles of Heat Transfer (Activate Learning wi…
Mechanical Engineering
ISBN:
9781305387102
Author:
Kreith, Frank; Manglik, Raj M.
Publisher:
Cengage Learning
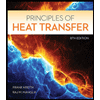
Principles of Heat Transfer (Activate Learning wi…
Mechanical Engineering
ISBN:
9781305387102
Author:
Kreith, Frank; Manglik, Raj M.
Publisher:
Cengage Learning