What are the disadvantages of MIG welding on stainless steels?
What are the disadvantages of MIG welding on stainless steels?

Before answering above question, we should know the physical and chemical properties of stainless steel compared to carbon steel, and how this affects the welding variables. Stainless steel is a Corrosion resistance steel due to Higher content of alloying elements ( Chromium & Nickle etc) in it as compare to carbon steel.
These alloying elements reduces the weld ability & have a more sluggish weld bead.
Stainless steel has lower thermal conductivity,
meaning that heat energy does not transfer or move away from the weld zone as fast. This is beneficial in welding, in that it therefore does not require as much current to achieve complete fusion because the heat is not being dissipating from the weld zone as rapidly.
Coefficient of thermal expansion for SS is about 50% more than carbon steel,
which could result in more distortion. Therefore, to help minimize warpage (particularly on sheet metal), weld at the lowest current possible, which still provides complete fusion between the wire and base plate.
Stainless steel also has lower electrical conductivity (i.e., higher electrical resistance). This means that wire feed speeds at the same rate as used with carbon steel will produce lower current levels with stainless steel.
In addition, maintaining a consistent contact tip to work distance (CTWD) is more critical with stainless steel, as variations result in a greater degree of change in current levels.
Now set these property differences into the various parameters require to MIG weld stainless steel.
First, the machine should be set on DC+ (direct current positive) polarity.
Regarding wire feed speed and voltage settings, most of MIG welding machine have a recommended settings for carbon steel (May not have settings for stainless steel).
Then as a starting point use the recommended settings for carbon steel, based on the thickness of the stainless steel sheet metal which you are welding.
Then adjust the settings from there to fine tune the weld.
1, Keep little higher wire feed speed rate than used with mild steel
2, Keep little lower current level 5%~10%
3, Use higher voltage settings, which will help wet out the puddle more, giving a flatter face and better wash-in at the toes of the weld.
**In general, the grade of wire use depends on the type of stainless steel base material you are welding.
Step by step
Solved in 3 steps

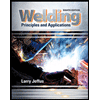
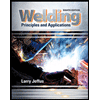