What is Job Costing?
Job costing is adhesive costs of each and every job involved in the production processes. It is an accounting measure. It is a method which determines the cost of specific jobs, which are performed according to the consumer’s specifications. Job costing is possible only in businesses where the production is done as per the customer’s requirement. For example, some customers order to manufacture furniture as per their needs.
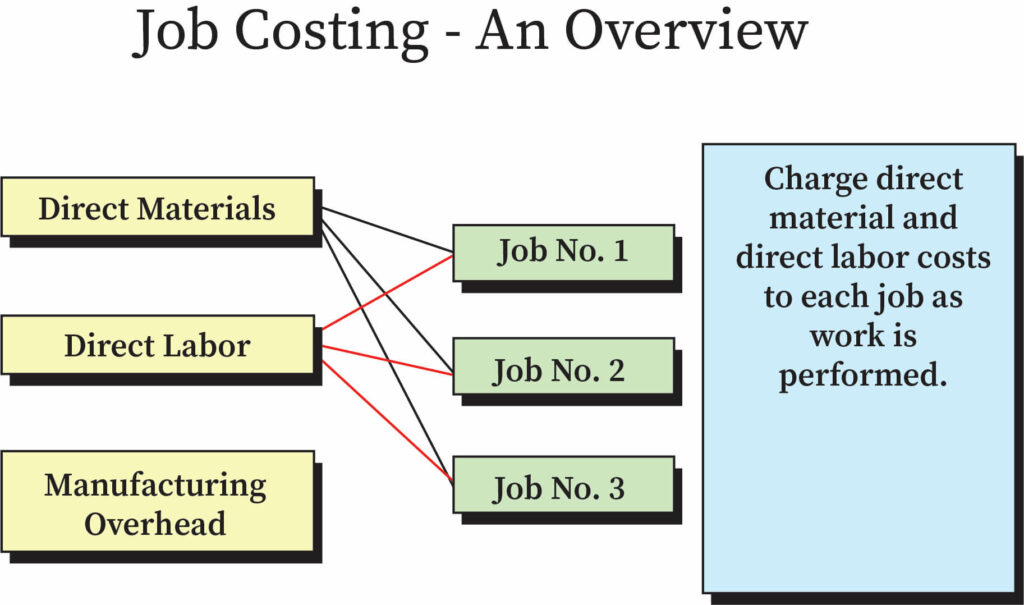
Features of Job costing
Following are some of the important features of job costing:
- Job costing helps to ascertain the profit and loss of each and every job in particular. This helps the management of the firms to identify the jobs which are more cost taking and which are cost saving. Also, the jobs which are profitable and which are less profitable.
- It helps in future planning of cost determined in the job. It helps the managers to estimate, plan, compare and control the costs involved in the job.
- Job costing helps to understand the various methods of calculation and avoid the long processes.
- Job costing method is used by various production firms as well as the service industry. For example: Various industries such as automobile garage, repair workshop, printing firms use job costing method. Many times products which are manufactured are not uniform in nature. In these situations, maintaining a separate record is helpful and time saving.
Advantages of Job costing
Following are some of the advantages of job costing:
- As job costing is to maintain account of different jobs separately, the profitability of each and every cost is separately known.
- Job costing helps to determine detailed cost analysis of various fields such as raw materials, labor and overhead of each job.
- Controlling efficiency is possible as individual jobs are given individual attention.
- Estimation of cost can be prepared easily in the job costing.
- The jobs which are not profitable can be avoided.
- Job costing helps the manufacturing units to provide precise quotes for each and every product.
Job costing documents
There are various documents used in job costing some are as follows:
1) Cost sheet : Cost sheet is a complete record of costs involved in various stages of production. Some producers combine the record of cost sheet and job order
2) Production order : This is an authorized document which is required by each and every manufacturing unit. Production order specifies the quantity of a product which constitutes the job.
3) Tools and spare order : Tools and spare order is the record of the tools and spares used in completing the job
4) Material requisition slip : It is a slip which indicates the materials demanded which are required for the job
5) Inspection order : This is the complete record of reviews involved in the job.
Process of job costing:
Following are the process involved in the job costing,
1) Enquiry : Manufacturers, before producing units, usually receive some inquiry from the customers such as price, quality, and time taken to produce a product.
2) Price estimation of the job : After receiving the enquiry, manufacturers estimate the costs involved in the job and compare whether this is based on the cost of execution of similar job previously and consider the possible changes in the various elements on the cost
3) Order : After estimation and price quotation, the producers receive the order. Each and every job is numbered in the job number order and a proper excel is prepared.
4) Preparation of production order : A production order is then prepared by the production control department. It is then sent to the concerned employee to carry out the job. The cost accountant prepares a proper job cost sheet in the spreadsheet form in order to determine the profit in each and every job. Production order consists of date on which order is prepared, job order number, description and number of products to be produced, date of start and completion of work, listing of materials, sequence of production process.
5) Design preparation : Sometimes a job involves customer specifications in special cases.
6) Dispatch of goods : This is the final process in which the final products are packed and delivered to the customers
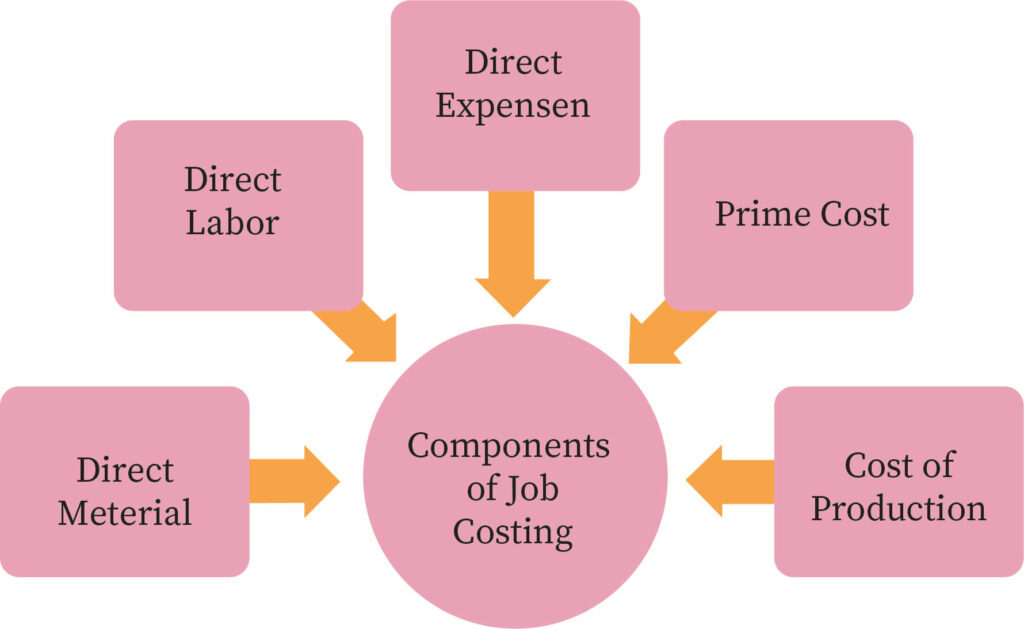
Accounting System of Job Costing
Job costing procedure and cost allocation for different activities involves different activities such as raw materials, labor and overhead. Following are activities involved in the different specification:
1) Material : Material is classified into direct and indirect materials. Direct materials are the raw materials which are required in the manufacturing process and indirect materials are materials which are not directly perceptible in the production process, for example, cleaning supplies. it involves 2 stages:
Stage 1: Procuring and storing the raw material into the warehouse
Stage 2: Picking up the raw materials from the store and issuing the same to the concerned job.
2) Direct labor cost : Laborers are directly involved in the production process of the job costing. The tool which takes into consideration the number of hours each and every employee’s work is called a Clock Card. It records the total time taken by each employee during the manufacturing process. Time ticket shows the date on which the job is completed. If the work is performed directly on the job, employees record the job number and then send it to the cost accounting department. The cost accountant then records pay rate and calculates the labor cost.
3) Direct expenses : direct expenses include cost of design, cost of hiring special tools and equipment, cost of tools.
4) Overhead expenses : The costs which are not directly related to direct labor material or production are termed as overhead expenses or factory overhead. Overhead expenses are calculated at the beginning of the year by estimating total overhead cost for the year and then divide by direct labor cost. It is charged in job costing as it is applied in overhead cost.
5) Job cost sheet : Manufacturing costs are recorded in the job cost sheet. This consists of necessary details about the job and cost involved in the production process. The companies follow specific forms to prepare a job cost sheet in which details like job number, customer number, supervisor name, number of units orders et cetera are prescribed.
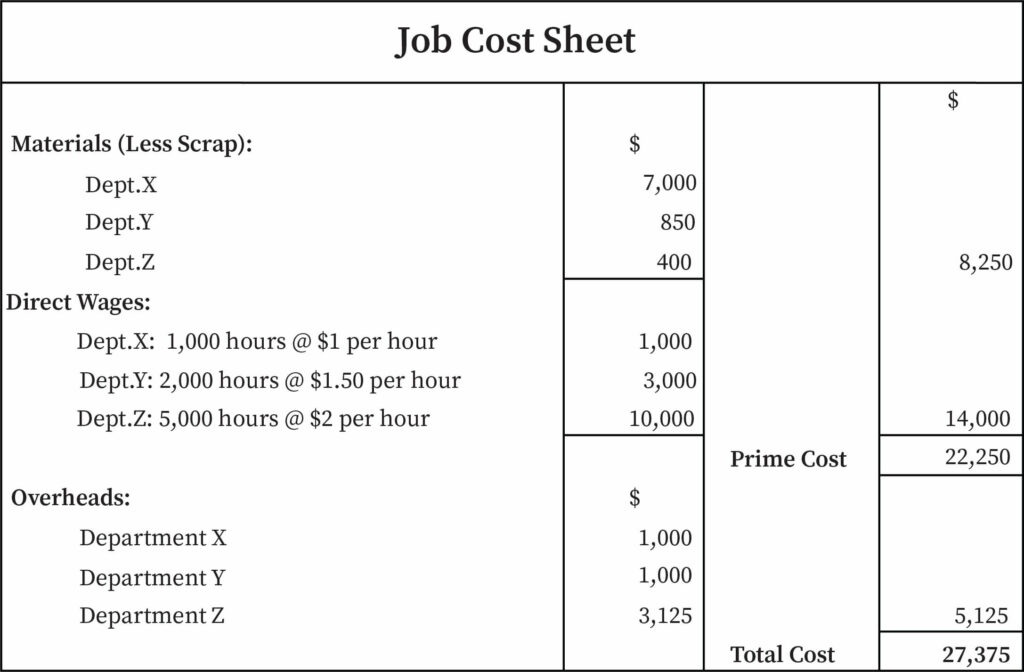
Limitations of job costing can be as follows:
- The job costing process sometimes becomes very lengthy and time consuming as separate spreadsheets or excels needs to be prepared for each and every job.
Context and Applications
This topic is significant in the professional exams for both undergraduate and graduate courses, especially for
- B.A Economics
- B.com
- CA
Want more help with your accounting homework?
*Response times may vary by subject and question complexity. Median response time is 34 minutes for paid subscribers and may be longer for promotional offers.
Search. Solve. Succeed!
Study smarter access to millions of step-by step textbook solutions, our Q&A library, and AI powered Math Solver. Plus, you get 30 questions to ask an expert each month.
Job Costing Homework Questions from Fellow Students
Browse our recently answered Job Costing homework questions.
Search. Solve. Succeed!
Study smarter access to millions of step-by step textbook solutions, our Q&A library, and AI powered Math Solver. Plus, you get 30 questions to ask an expert each month.