Benefits of Switching to JIT You have recently been hired as the management accountant forDelta Technologies Inc. The company produces a broad line of subassemblies that are used in theproduction of flat-screen TVs and other electronic equipment. Competitive pressures, principallyfrom abroad, have caused the company to reexamine its competitive strategy and associated management accounting and control systems. More to the point, the company feels a pressing need to adoptJIT manufacturing, to improve the quality of its outputs (in response to ever-increasing demands byconsumers of electronic products), and to better manage its cost structure.A year ago, Delta acquired, via a 5-year lease, new manufacturing equipment, the annual cost ofwhich is $500,000. To support the move to JIT, however, Delta would have to acquire new, computercontrolled manufacturing equipment, the leasing cost of which is estimated at $1 million per year for4 years. If the company were to break its existing lease it would incur a one-time penalty of $275,000.The replacement equipment is expected to provide significant decreases in variable manufacturing cost per unit, from $50 to $35. This reduction is attributed to faster setup times with the newmachine, faster processing speed, a reduction in direct material waste, and a reduction in direct laborexpenses (because of increased automation). In addition, improvements in manufacturing cycle timeand improvements in product quality are expected to increase annual sales (in units) by approximately 25% (based on a current volume of 40,000 units).Additional financial information regarding each decision alternative (existing equipment versusreplacement equipment) is as follows:[LO 17-2, 17-4][LO 17-1, 17-2,17-5, 17-6]ProblemsItem Pre-JIT Post-JITSelling cost per unit $ 5.00 $ 5.00Average per-unit cost of Direct Materials Inventory 15.00 12.00Average per-unit cost of WIP Inventory 25.00 20.00Average per-unit cost of Finished Goods Inventory 40.00 30.00Selling price per unit 70.00 70.00Final PDF to printerblo17029_ch17_713-774.indd 766 02/19/18 09:10 AM766 Part Three Operational-Level ControlThe increased automation, including computer-based manufacturing controls, associated withthe replacement equipment will greatly reduce the need for inventory holdings. The annual inventory holding cost, based on the company’s (after-tax) weighted-average cost of capital, is 10%.Based on engineering estimates provided to Delta by the lessor company, all inventory holdings(direct materials, WIP, and finished goods) can safely be cut in half from current levels. Currently,Delta holds, on average, 4 months of raw materials inventory, 3 months of WIP inventory, and 2months of finished goods inventory—all of which are based on production requirements.Required1. Essentially, how is a JIT manufacturing system different from a conventional system?2. What is an appropriate role for management accounting regarding a company’s adoption of a JIT manufacturing system?3. Based on the information presented above, determine the annual financial benefit (including reductionin inventory carrying costs) associated with the proposed move by the company to JIT. (Round yourfinal answer to the nearest whole dollar.)4. What is the projected first-year net financial effect of investing in the new equipment in conjunctionwith a move to JIT? Based on an analysis of financial considerations alone, should the company makethe switch to JIT? Why or why not?5. What additional considerations (both qualitative and quantitative) might bear on the decision at hand?
Benefits of Switching to JIT You have recently been hired as the management accountant for
Delta Technologies Inc. The company produces a broad line of subassemblies that are used in the
production of flat-screen TVs and other electronic equipment. Competitive pressures, principally
from abroad, have caused the company to reexamine its competitive strategy and associated management accounting and
JIT manufacturing, to improve the quality of its outputs (in response to ever-increasing demands by
consumers of electronic products), and to better manage its cost structure.
A year ago, Delta acquired, via a 5-year lease, new manufacturing equipment, the annual cost of
which is $500,000. To support the move to JIT, however, Delta would have to acquire new, computercontrolled manufacturing equipment, the leasing cost of which is estimated at $1 million per year for
4 years. If the company were to break its existing lease it would incur a one-time penalty of $275,000.
The replacement equipment is expected to provide significant decreases in variable
machine, faster processing speed, a reduction in direct material waste, and a reduction in direct labor
expenses (because of increased automation). In addition, improvements in manufacturing cycle time
and improvements in product quality are expected to increase annual sales (in units) by approximately 25% (based on a current volume of 40,000 units).
Additional financial information regarding each decision alternative (existing equipment versus
replacement equipment) is as follows:
[LO 17-2, 17-4]
[LO 17-1, 17-2,
17-5, 17-6]
Problems
Item Pre-JIT Post-JIT
Selling cost per unit $ 5.00 $ 5.00
Average per-unit cost of Direct Materials Inventory 15.00 12.00
Average per-unit cost of WIP Inventory 25.00 20.00
Average per-unit cost of Finished Goods Inventory 40.00 30.00
Selling price per unit 70.00 70.00
Final PDF to printer
blo17029_ch17_713-774.indd 766 02/19/18 09:10 AM
766 Part Three Operational-Level Control
The increased automation, including computer-based manufacturing controls, associated with
the replacement equipment will greatly reduce the need for inventory holdings. The annual inventory holding cost, based on the company’s (after-tax) weighted-average cost of capital, is 10%.
Based on engineering estimates provided to Delta by the lessor company, all inventory holdings
(direct materials, WIP, and finished goods) can safely be cut in half from current levels. Currently,
Delta holds, on average, 4 months of raw materials inventory, 3 months of WIP inventory, and 2
months of finished goods inventory—all of which are based on production requirements.
Required
1. Essentially, how is a JIT manufacturing system different from a conventional system?
2. What is an appropriate role for management accounting regarding a company’s adoption of a JIT manufacturing system?
3. Based on the information presented above, determine the annual financial benefit (including reduction
in inventory carrying costs) associated with the proposed move by the company to JIT. (Round your
final answer to the nearest whole dollar.)
4. What is the projected first-year net financial effect of investing in the new equipment in conjunction
with a move to JIT? Based on an analysis of financial considerations alone, should the company make
the switch to JIT? Why or why not?
5. What additional considerations (both qualitative and quantitative) might bear on the decision at hand?

Trending now
This is a popular solution!
Step by step
Solved in 3 steps

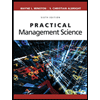
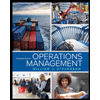
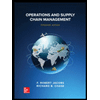
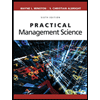
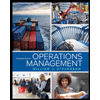
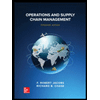
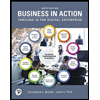
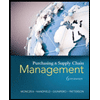
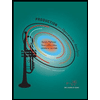