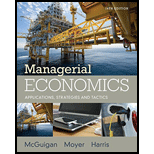
Concept explainers
a
To find:
a

Explanation of Solution
The annual capacity of plants A, B, and C are 75,000, 150,000, and 350,000 units, respectively. Production beyond annual capacities requires multiple plants of the same type. And hence, the fixed costs would increase by the same multiples too.
Unit variable costs are $9, $8 and $7 for plant A, B, and C, respectively.
The schedule below shoes the average total cost for Plant A for varying output levels.
Q |
VC (1) |
FC (2) |
TC (1)+(2) |
ATC |
25,000 |
$9(25,000) =$225,000 |
$150,000 |
$375,000 |
$15 |
50,000 |
$9(50,000) =$450,000 |
$150,000 |
$600,000 |
$12 |
75,000 |
$9(75,000) =$675,000 |
$150,000 |
$825,000 |
$11 |
100,000 |
$9(100,000) =$900,000 |
2($150,000) =$300,000 |
$1,200,000 |
$12 |
125,000 |
$9(125,000) =$1,125,000 |
2($150,000) =$300,000 |
$1,425,000 |
$11.40 |
150,000 |
$9(150,000) =$1,350,000 |
2($150,000) =$300,000 |
$1,650,000 |
$11 |
175,000 |
$9(175,000) =$1,575,000 |
3($150,000) =$450,000 |
$2,025,000 |
$11.57 |
200,000 |
$9(200,000) =$1,800,000 |
3($150,000) =$450,000 |
$2,025,000 |
$11.25 |
225,000 |
$9(225,000) =2,025,000 |
3($150,000) =$450,000 |
$2,475,000 |
$11 |
250,000 |
$9(250,000) =$2,250,000 |
4($150,000) =$600,000 |
$2,850,000 |
$11.40 |
275,000 |
$9(275,000) =$2,475,000 |
4($150,000) =$600,000 |
$3,075,000 |
$11.18 |
300,000 |
$9(300,000) =$2,700,000 |
4($150,000) =$600,000 |
$3,300,000 |
$11 |
325,000 |
$9(325,000) =$2,925,000 |
5($150,000) =$750,000 |
$3,675,000 |
$11.31 |
350,000 |
$9(350,000) =$3,150,000 |
5($150,000) =$750,000 |
$3,900,000 |
$11.14 |
The schedule below shows the average total cost for Plant B for varying output levels.
Q | VC(1) | FC(2) | TC(1)+(2) | ATC |
25,000 |
$8(25,000) =$200,000 |
$250,000 |
$450,000 |
$18 |
50,000 |
$8(50,000) =$400,000 |
$250,000 |
$650,000 |
$12 |
75,000 |
$8(75,000) =$600,000 |
$250,000 |
$850,000 |
$11.33 |
100,000 |
$8(100,000) =$800,000 |
$250,000 |
$1,050,000 |
$10.50 |
125,000 |
$8(125,000) =$1,000,000 |
$250,000 |
$1,250,000 |
$10 |
150,000 |
$8(150,000) =$1,200,000 |
$250,000 |
$1,450,000 |
$9.67 |
175,000 |
$8(175,000) =$1,400,000 |
2($250,000) =$500,000 |
$1,900,000 |
$10.86 |
200,000 |
$8(200,000) =$1,600,000 |
2($250,000) =$500,000 |
$2,100,000 |
$10.50 |
225,000 |
$8(225,000) =$1,800,000 |
2($250,000) =$500,000 |
$2,300,000 |
$10.22 |
250,000 |
$8(250,000) =$2,000,000 |
2($250,000) =$500,000 |
$2,500,000 |
$10 |
275,000 |
$8(275,000) =$2,200,000 |
2($250,000) =$500,000 |
$2,700,000 |
$9.82 |
300,000 |
$8(300,000) =$2,400,000 |
2($250,000) =$500,000 |
$2,900,000 |
$9.67 |
325,000 |
$8(325,000) =$2,600,000 |
3($250,000) =$750,000 |
$3,350,000 |
$10.31 |
350,000 |
$8(350,000) =$2,800,000 |
3($250,000) =$750,000 |
$3,550,000 |
$10.14 |
The schedule below shows the average total cost for Plant C for varying output levels.
Q | VC(1) | FC(2) | TC(1)+(2) | ATC |
25,000 |
$7(25,000) =$175,000 |
$450,000 |
$625,000 |
$25 |
50,000 |
$7(50,000) =$350,000 |
$450,000 |
$800,000 |
$16 |
75,000 |
$7(75,000) =$525,000 |
$2450,000 |
$975,000 |
$13 |
100,000 |
$7(100,000) =$700,000 |
$450,000 |
$1,150,000 |
$11.50 |
125,000 |
$7(125,000) =$875,000 |
$450,000 |
$1,325,000 |
$10.60 |
150,000 |
$7(150,000) =$1,050,000 |
$450,000 |
$1,500,000 |
$10 |
175,000 |
$7(175,000) =$1,225,000 |
$450,000 |
$1,675,000 |
$9.57 |
200,000 |
$8(200,000) =$1,600,000 |
$450,000 |
$2,850,000 |
$9.25 |
225,000 |
$7(225,000) =$1,575,000 |
$450,000 |
$2,025,000 |
$9 |
250,000 |
$7(250,000) =$1,750,000 |
$450,000 |
$2,200,000 |
$8.80 |
275,000 |
$7(275,000) =$1,925,000 |
$450,000 |
$2,375,000 |
$8.64 |
300,000 |
$8(300,000) =$2,100,000 |
$450,000 |
$2,550,000 |
$8.50 |
325,000 |
$7(325,000) =$2,275,000 |
$450,000 |
$3,725,000 |
$8.38 |
350,000 |
$7(350,000) =$2,450,000 |
$450,000 |
$3,900,000 |
$8.29 |
Introduction:
Fixed costs (FC) are the costs that the firm has to incur irrespective of the level of output.
Variable costs (VC) are the costs that vary with the level of output, that is, increase as the output level increases, and vice versa.
Total cost (TC) is the total cost incurred by the firm in the production process. It is the sum of fixed cost and variable cost.
Average total cost
b)
To ascertain:Long run average total cost schedule.
b)

Explanation of Solution
The combined long-run average cost schedule for three plants is as given below:
Q |
Long Run ATC |
25,000 | $15 |
50,000 | $12 |
75,000 | $11 |
100,000 | $10.50 |
125,000 | $10 |
150,000 | $9.67 |
175,000 | $9.57 |
200,000 | $9.25 |
225,000 | $9 |
250,000 | $8.80 |
275,000 | $8.64 |
300,000 | $8.50 |
325,000 | $8.38 |
350,000 | $8.29 |
For output level beyond 75,000 units (production capacity of plant A), average total cost is lower for plant B. Similarly, for output level beyond 150,000 units (production capacity of plant B), average total cost is lower for plant C.
Introduction:
Fixed costs (FC) are the costs that the firm has to incur irrespective of the level of output.
Variable costs (VC) are the costs that vary with the level of output, that is, increase as the output level increases, and vice versa.
Total cost (TC) is the total cost incurred by the firm in the production process. It is the sum of fixed cost and variable cost.
Average total cost
Want to see more full solutions like this?
Chapter 8 Solutions
Managerial Economics: Applications, Strategies and Tactics (MindTap Course List)
- Shawn Pen & Pencil Sets Inc. has fixed costs of $421,400. Its product currently sells for $18 per unit and has variable costs of $8.20 per unit. Mr. Bic, the head of manufacturing, proposes to buy new equipment that will cost $440,000 and drive up fixed costs to $563,500. Although the price will remain at $18 per unit, the increased automation will reduce costs per unit to $5.75. a. Compute the following break-even points: i. Current break-even point ii. Proposed new break-even point b. As a result of Bic's suggestion, will the break-even point go up or down?arrow_forwardPlease examine the table below. What is the Average Total Cost (ATC) of the fourth unit? Total Output Cost $100 1 $150 $185 $245 4. $335 $485 6 $710 $335 About $167.50 About $90 About $83.75arrow_forwardYou are a manager at Glass Inc. — a mirror and window supplier. Recently, you conducted a study of the production process for your single-side encapsulated window.The results from the study are summarized below and are based on the 8 units of capital currently available at your plant. Workers are paid $ 60 per unit, per unit capital costs are $ 20, and your encapsulated windows sell for $ 12 each. Given this information, optimize your human resource and production decisions. Find a profit you earn. Labor Output 0 0 1 10 2 thirty 3 60 4 80 5 90 6 95 7 95 8 90 9 80 10 60arrow_forward
- A division of Ditton Industries manufactures a deluxe toaster oven. Management has determined that the daily marginal cost function associated with producing these toaster ovens is given by C'(x) = 0.0003x2−0.18x + 21 where C '(x) is measured in dollars/unit and x denotes the number of units produced. Management has also determined that the daily fixed cost incurred in the production is $800. (a) Find the total cost incurred by Ditton in producing the first 300 units of these toaster ovens per day. (b) What is the total cost incurred by Ditton in producing the 201st through 300th units/day?arrow_forwardGreen Gardens Berry Farms is facing some harvesting decisions in order to decide how many tons of berries to harvest and supply to local markets. They face the following situation: Their FIXED COSTS in terms of existing harvesting tools, land rents, etc. is: $20 Their main variable cost is to hire farmworkers, whom they must pay as per the region's minimum living wage laws at $15 per worker hour. They are able to coordinate production given their existing infrastructure at the following cost structure. Berry harvests are measured in Metric Tons harvested per worker hour. Green Gardens Berry Farm Quantity of Farmworker quantity in metric tons harvested) hours needed for Harvest 1. 3 2. 13 4. 14 20arrow_forwardMarginal Cost A division of Ditton Industries manufactures a deluxe toaster oven. Management has determined that the daily marginal cost function associated with producing these toaster ovens is given by C'(x) = 0.0006x2 − 0.14x + 22 where C'(x) is measured in dollars per unit and x denotes the number of units produced. Management has also determined that the daily fixed cost incurred in the production is $900. (a)Find the total cost incurred by Ditton in producing the first 300 units of these toaster ovens per day. (b) What is the total cost incurred by Ditton in producing the 201st through 300th units/day?arrow_forward
- A manufacturing plant has a potential production capacity of 1,000 units per month (capacity can be increased by 10 percent if subcontractors are employed). The plant is normally operated at 80 percent capacity. Operating the plant above this level significantly increases variable costs per unit because of the need to pay the skilled workers higher overtime wage rates. For all output levels up to 80 percent capacity, variable cost per unit is $100. Above 80 percent and up to 90 percent, variable costs on this additional output increase by 10 percent. When output is above 90 percent and up to 100 percent capacity, the additional units costs an additional 25 percent over the unit variable costs for outputs up to 80 percent capacity. For production above 100 percent capacity and up to 110 percent of capacity, extensive subcontracting work is used and the unit variable costs of these additional units are 50 percent above those at output levels up to 80 percent of capacity. At 80 percent…arrow_forwardMatch each cost term to its definition. Fixed cost V [Choose ] all costs that are incurred over the life of a product, process, or service expenses that are anticipated and occur at regular intervals Variable cost money already spent based on a past decision depends on the level of output or activity associated with using a resource in one activity instead of another Sunk cost remains constant (unchanged) regardless of the level of output Opportunity cost [ Choose ] Recurring costs [ Choose ] Life-cycle costs [ Choose ]arrow_forwardParadise Pottery had the following costs in May when production is 800 ceramic pots: materials, $8,700; labor (variable), $2,900; depreciation, $1,100; rent, $900; and other fixed costs, $1,500. If production changes to 900 units, how much will the total variable costs and total fixed costs be, respectively?arrow_forward
- Antoine rents rooms in his hotel for an average of $100 per night. The variable cost per rented room is $20, to cover maid service and utilities. His fixed costs are $100,000 and his profit last year was $20,000. For Antoine, the contribution per unit is $100 $80 $1005 $800arrow_forwardABC Company is the manufacturer of a low-noise air-purification system. Its current capacity is 10,000 units/month, but ABC received orders totaling 9,000 units each month. Currently, ABC sells its system at a price of $200 per unit, its fixed cost is $500,000/month, and its variable cost is $100/unit. Note that currently, half of ABC’s variable cost is materials, and the other half is labor cost (wages for workers). ABC wants to consider cutting its price by 10% to stimulate demand. If ABC expands its capacity, it will have to lease additional manufacturing machines, each of which will cost $20,000/month to lease and can add 1000 units to ABC’s capacity. All existing workers are already working full-time. So, if ABC expands production, ABC has to either pay existing employees for overtime (1.5 times the regular wages) or hire new workers, who are expected to be paid 90% of the hourly wage of existing workers but produce only 75% of the hourly output of existing workers. (a) What is…arrow_forwardAverage Total Cost ($ per tablet) Number of Factories Q=100 Q=200 Q=300 Q=400 Q=500 Q=600 1 400 300 200 240 300 720 540 350 180 160 250 540 3 720 400 170 160 200 360 The company Ride is a major manufacturer of bicycles. Currently the company produces bikes using only one factory. However it is considering expanding production to two or even three factories. The following table shows the company's short-run average total cost (SRATC) each month for various levels of production if it uses one two or three factories. (Note: Q equals the total quantity of bikes produced by all factories.) Refer to the table. Which of the following is NOT true about the long-run average cost curve of Ride's bikes? Ride experiences economies of scale at any quantity less than 400 bikes. Ride experiences economies of scale at any quantity over 300 bikes. The long-run average total cost of production per bike will be $170 when 300 bikes are produced in the long run. The long-run average total cost of…arrow_forward
- Managerial Economics: Applications, Strategies an...EconomicsISBN:9781305506381Author:James R. McGuigan, R. Charles Moyer, Frederick H.deB. HarrisPublisher:Cengage LearningManagerial Economics: A Problem Solving ApproachEconomicsISBN:9781337106665Author:Luke M. Froeb, Brian T. McCann, Michael R. Ward, Mike ShorPublisher:Cengage Learning
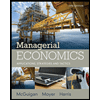
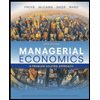